Comparison of belt conveyor Drive Methods
1. Electric roller
The built-in electric drum has poor heat dissipation because the motor is installed inside the drum. It is generally used on belt conveyors with a power of less than 30kw and a length of less than 150m. Because the motor is installed outside the drum, the external electric drum has better heat dissipation. It is generally used on belt conveyors with a power of less than 45kw and a length of less than 150m.
Advantages: compact structure, low maintenance costs, high reliability, the driving device and the transmission roller are integrated into one.
Disadvantages: Poor soft start performance, large impact on the power grid when the motor starts. The reliability is worse than the Y-type motor + coupling + reducer drive method.
2. Poor driving mode of Y-type motor + coupling + reducer
Advantages: simple structure, small maintenance workload, low maintenance costs and high reliability.
Disadvantages: Poor soft start performance, large impact on the power grid when the motor starts. Generally used on belt conveyors with a power of less than 45kw and a length of less than 150m.
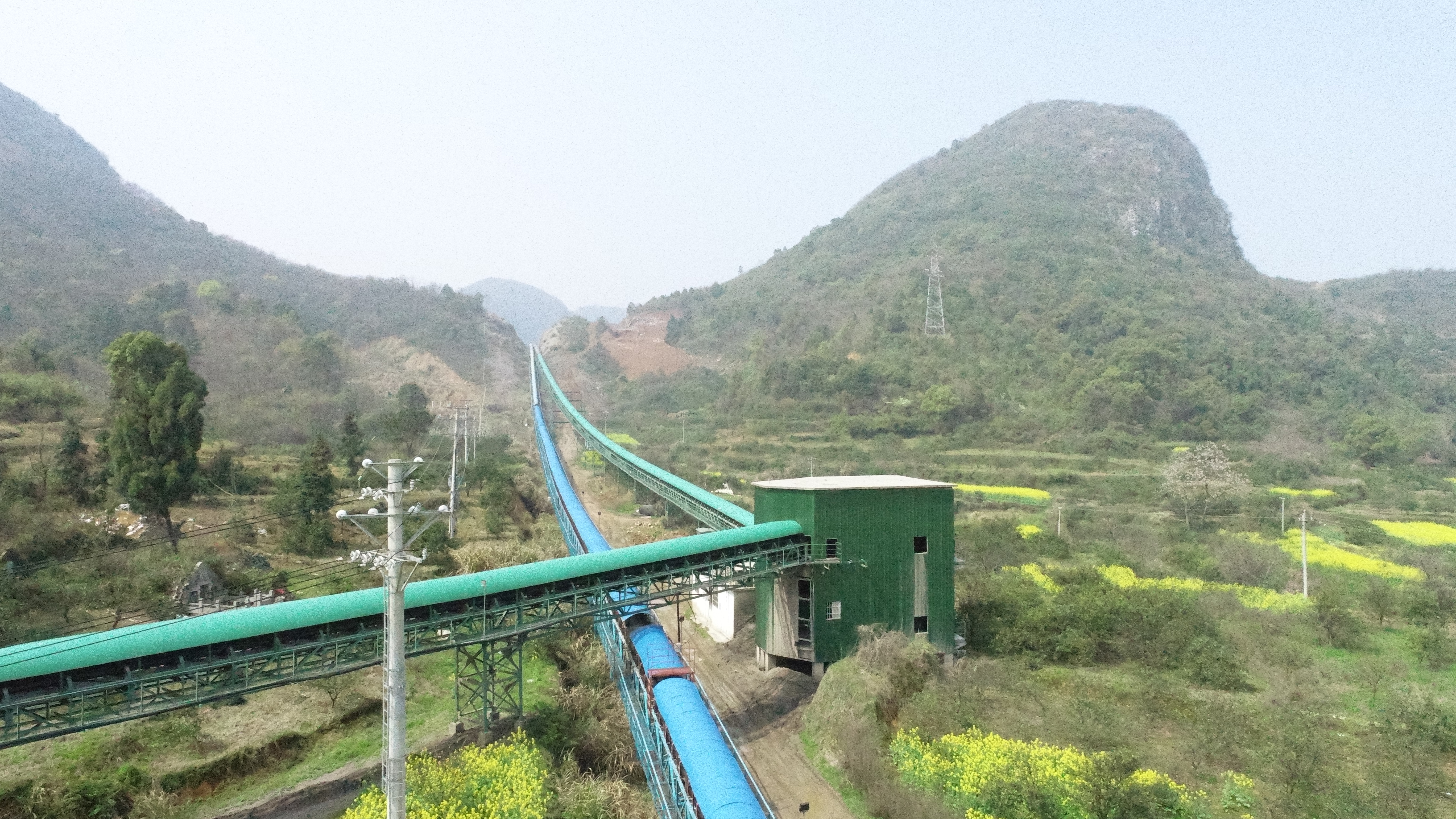
It is a widely used driving device on belt conveyors. It is generally used on belt conveyors with a single machine power of less than 630kw and a length of less than 1500m.
The torque-limiting hydraulic coupling is divided into a torque-limiting hydraulic coupling with a rear auxiliary chamber and a torque-limiting hydraulic coupling without a rear auxiliary chamber. Since the hydraulic oil slowly enters the working chamber of the hydraulic coupling from the rear auxiliary chamber through the throttle hole when the motor is started, its starting performance is better than that of the latter.
1) If you choose one with a rear auxiliary chamber, when there are two models of hydraulic couplings that can meet the transmission power, because this type of hydraulic coupling takes a long time to start and generates a lot of heat, the larger model should be given priority. Force coupling.
2) If you choose one without a rear auxiliary chamber, when there are two models of hydraulic coupling that can meet the transmission power, because this type of hydraulic coupling has a shorter start-up time and a smaller calorific value, the smaller one should be given priority. Model fluid coupling.
3) For belt conveyors driven by multiple motors, if this drive method is selected, it is recommended that the hydraulic coupling be a torque-limiting hydraulic coupling with a rear auxiliary chamber.
Advantages: high cost performance, simple and compact structure, small maintenance workload, low repair costs, protection of motor overload, ability to balance motor power when driven by multiple motors, delay start in separate units, reducing the impact on the power grid when the belt conveyor starts impact, high reliability and low price, it is the preferred driving method for belt conveyors with a length less than 1500m.
Disadvantages: The soft start performance is poor, and it is not suitable for downward transport belt conveyors and belt conveyors that require speed regulation function.
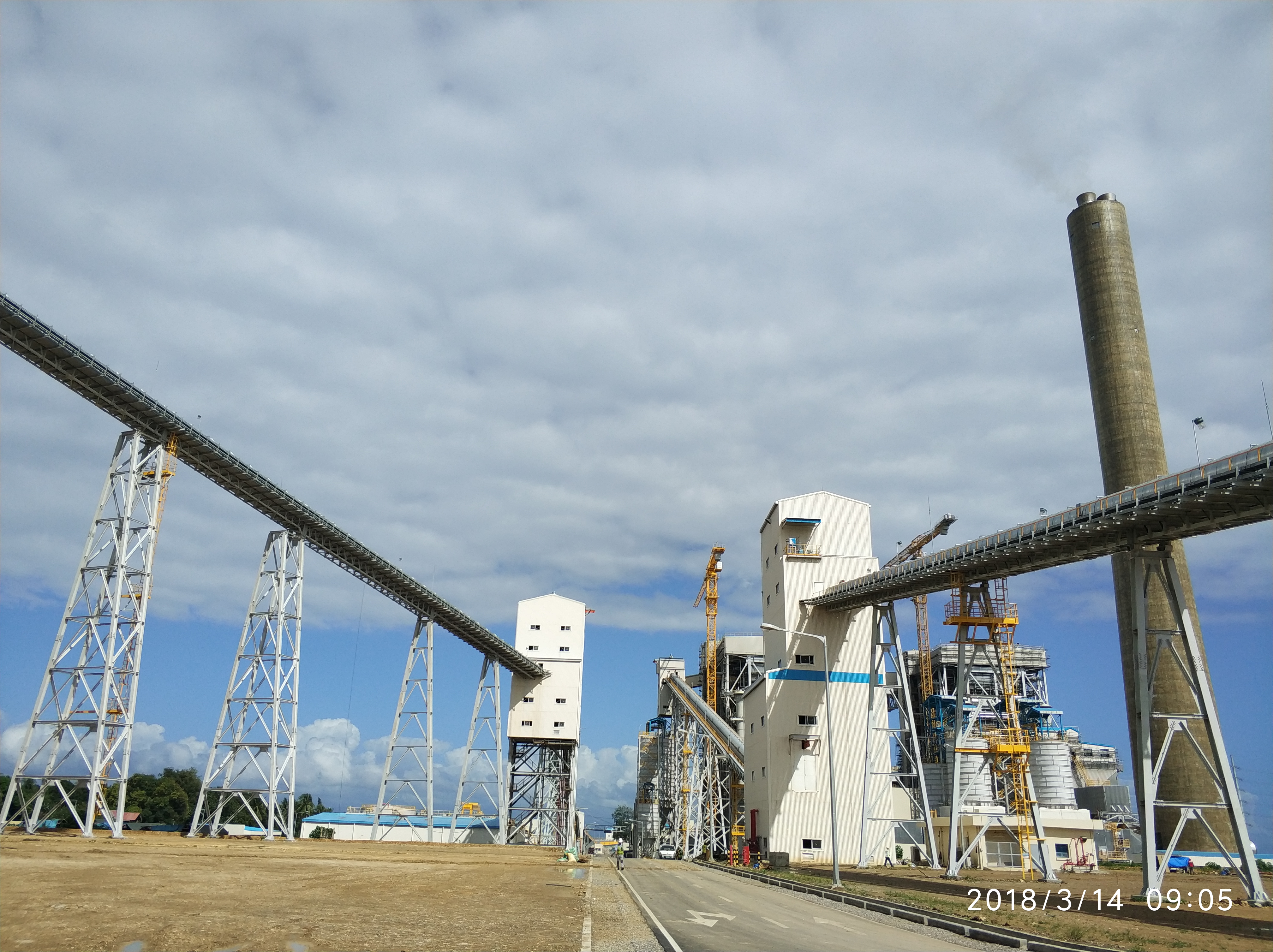
A commonly used driving method for large belt conveyors. It is generally used on long-distance large belt conveyors with a length of more than 800m.
Advantages: Simple structure, less overload maintenance workload, motor no-load start, protection of motor overload, when multiple motors are driven, they can be started in separate stages to reduce the impact on the power grid when the belt conveyor is started, reliability It is higher, has better soft-start performance, has controllable start-up performance, that is, the start-up time is controllable, the start-up speed curve is controllable, and the price is low.
Disadvantages: When the hydraulic coupling is started, because the oil volume change in the working chamber of the hydraulic coupling and the speed change curve are non-linear and have backwardness, the controllability dynamic response is slow, and closed-loop control is difficult. Sometimes Oil leakage occurs. It is not suitable for use on lower Conveyor Belts and belt conveyors that require speed regulation function.